Das ist mal ein reißerischer Titel, oder? Wie kann man mit externen MOSFETs die Brandgefahr mindern? Was sind überhaupt MOSFETs? Was hat das mit meinem 3D-Drucker zu tun? Warum überhaupt Brandgefahr? Und bin ich auch nur wieder einer dieser Leute, die laufend geistige Brandstiftung betreiben, um jemanden wie Dich dazu zu bekommen, Produkte zu kaufen – um selbst an den Provisionen mitzuverdienen? Urteile selbst!
Hier ist das Thema:
In meinem AnyCubic i3 Mega 3D Drucker steckt ein Mainboard, das die komplette Steuerung sämtlicher Komponenten übernimmt. Dabei handelt es sich um ein 8-Bit Trigorilla Board. Hier mal zur Veranschaulichung das Pinout:
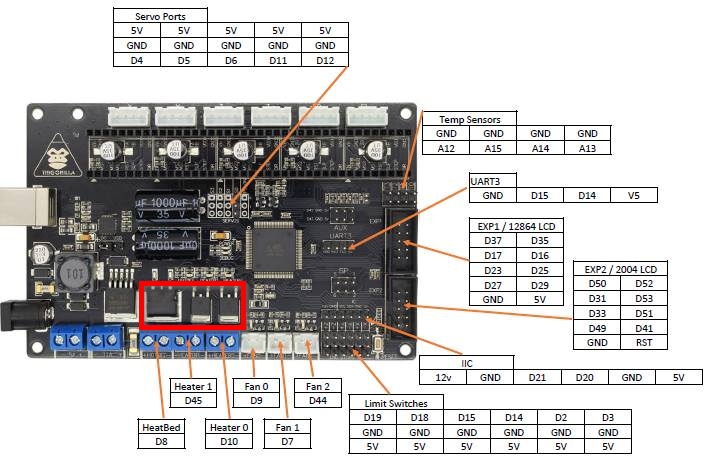
Besonders interessant sind die Anschlüsse D10, D45 und D8. Genauer: Heater0, Heater1 und HeatBed. An Heater0 und Heater1 liegen die Stromversorgungen für maximal zwei Hotends und an HeatBed die Stromversorgung für die Heizmatte vom Druckbett. Da der AnyCubic i3 Mega nur über ein Hotend verfügt, ist üblicherweise nur Heater0 belegt. Bei meinem Drucker allerdings hat sich der MOSFET an D10 verabschiedet, weshalb mein Hotend an Heater1 anliegt und ich der Einfachheit halber die Belegung in der Firmware vertauscht habe. 🙂
MOSFET
Was also ist überhaupt ein MOSFET? Zunächst einmal steht die Abkürzung für: Metal Oxide Semiconductor Field Effect Transistor oder auf Deutsch: Metall-Oxid-Halbleiter-Feldeffekttransistor. Wenn Du zum Experten werden willst, dann kannst Du jetzt nach weiteren Details suchen (z.B. hier und ja, das MOS in MOS Technology kommt auch daher). Für den Scope dieses Artikels reicht es zu wissen, dass es sich dabei um eine Art “Schalter” handelt. Die Idee: Der Transistor kann einen Stromkreis mit einer hohen Spannung schließen, indem man eine kleine Spannung anlegt. Dazu hat er üblicherweise drei Beinchen, die korrekt angeschlossen werden müssen.
Beim HotEnd und beim HeatBed kannst Du Dir das so vorstellen, dass, sobald der Drucker z.B. über den Temperatur-Sensor des HeatBeds gemeldet bekommt, dass das Bett (noch) keine Zieltemperatur von bspw. 60°C erreicht hat, das Board eine kleine Spannung an den Transistor anlegt der mit D8 verbunden ist und somit einen Stromkreis schließt, der eine hohe Spannung an das HeatBed anlegt. Ergebnis: Das Bett heizt sich auf. Irgendwann übersteigt es die 60°C und der “Schalter” öffnet den Stromkreis, um das Heizen abzuschalten. Das Heizbett kühlt sich also wieder ab und sobald es unter 60°C fällt, wird der Stromkreis erneut geschlossen, usw. usf.
Solche Schaltvorgänge können relativ oft passieren – das Ziel ist es ja, dass die Temperatur konstant gehalten wird. Der Drucker kennt dazu Algorithmen, die darauf optimiert sind das wirklich gut hinzubekommen. Hier noch mal für Dich als zukünftigen Experten: PID-Einstellungen sind dabei das entsprechende Stichwort und mehr darüber erfährst Du hier.
Das Problem: Viele Schaltvorgänge und hohe Ströme sorgen nun dafür, dass der Transistor sich aufheizt. Ähnliche Transistoren, die bspw. als Spannungsregler verwendet werden, haben daher oft einen kleinen Kühlkörper huckepack. Die MOSFETs aber auf dem Trigorilla Board haben… nichts dergleichen. Und die Gefahr ist, dass sie bei einer großen Belastung irgendwann hops gehen und im schlimmsten Fall gleich das ganze Board mitnehmen.
Klemmen oder Löten
Ein weiteres Problem ist, dass die stromführenden Adern, die in den blauen Schraubklemmen auf dem Board stecken, von AnyCubic nicht mit passenden Aderendhülsen gecrimpt wurden, sondern verzinnt und dann gequetscht. Das kann man machen… in Deutschland würde das so vermutlich aber nicht durchgehen. Das hat etwas damit zu tun, dass sich auch die Kabel erwärmen und damit das Zinn weich werden kann. Das kann zu Funkenschlag führen, lässt die Isolierung anschmoren und zum Schluss brennt einem die Hütte ab.
Es kursieren viele Geschichten im Internet von Wohnungen, die aufgrund minderwertig konstruierter 3D Drucker abgebrannt sind. Von daher stellt sich halt die Frage: Wie mit externen MOSFETs die Brandgefahr mindern?
Nun: Zunächst einmal wäre es wichtig zu verstehen, dass jeglicher Eingriff in die Elektronik Deines 3D Druckers potentiell sehr gefährlich sein kann. Du solltest wissen, was Du tust; ich übernehme keinerlei Haftung und dieser Artikel dokumentiert im Grunde genommen lediglich meine eigenen Erkenntnisse. Und falls sie Dir dabei helfen, Deine eigenen Projekte umzusetzen, freut mich das – und es geschieht auf Dein eigenes Risiko.
That being said:
Externe (passiv gekühlte) MOSFETs entlasten das Trigorilla-Board und in Kombination mit korrekt gecrimpten Adern verringerst Du damit potentielle Risiken wie bspw. Schmorbrände oder ein vorzeitiges Ableben Deines 3D Druckers. Außerdem bringt es Spaß, an seinen Werkzeugen zu basteln. 🙂
Adapter
Das Gehäuse vom AnyCubic i3 Mega ist zu einem Viertel leer. Das ist genial, weil sich dadurch so einiges einbauen lässt. Hier also mal eine Impression für eine Doppel-MOSFET-Konfiguration, die meinen Drucker nun aufwertet:
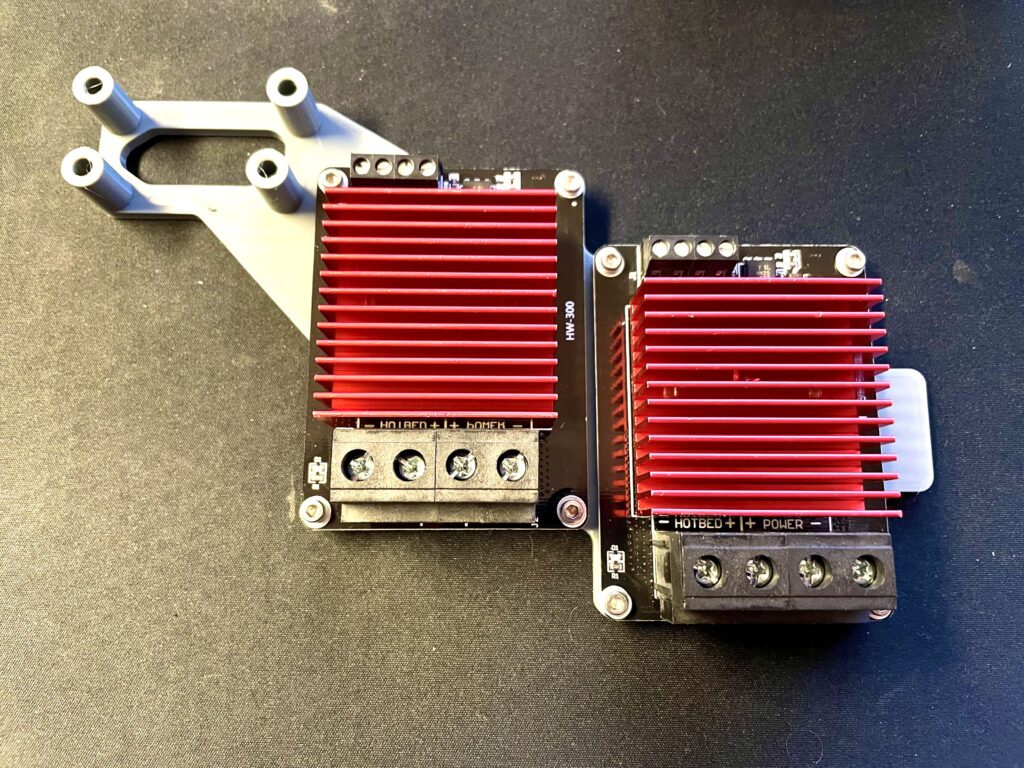
Die MOSFETs habe ich über Amazon gekauft (Link) und den Halter bekommst Du bei thingiverse. An dieser Stelle ein Hinweis: Um die MOSFET Platinen auf die Adapterplatte zu schrauben, benötigst Du acht M3x10 Schrauben und idealerweise passende M3 Unterlegscheiben. Die Idee ist es dann, dass Du im AnyCubic i3 Mega die Breakout-Platine mit dem SD-Kartenleser abschraubst, die Adapterplatte über die Abstandshalter schiebst und dann die Platine wieder draufschraubst. Fertig.
![]() | ![]() |
Genial, oder?
Und danach geht es auch schon los mit der Verkabelung: Der von oben betrachtet linke MOSFET soll das HotEnd schalten, der rechte das HeatBed. Die oberen Schraubklemmen werden mit dem Trigorilla Board verbunden, die unteren jeweils rechten Klemmen mit dem Netzteil und die jeweils linken mit dem HotEnd und dem HeatBed. Die Kabel für das HotEnd stecken dabei in Schraubklemmen am Breakout-Board, an dem alle Kabel auch von Außen drangesteckt werden, und das Kabel vom HeatBed verläuft durch ein Loch im Gehäuse direkt nach draußen und endet an der Heizmatte (zusammen mit dem Sensorkabel).
Hier eine ablenkungsfreie Draufsicht – interpretationsfrei und mit der Präzision eines gelernten Elektrikers ebenbürtig gezeichnet:
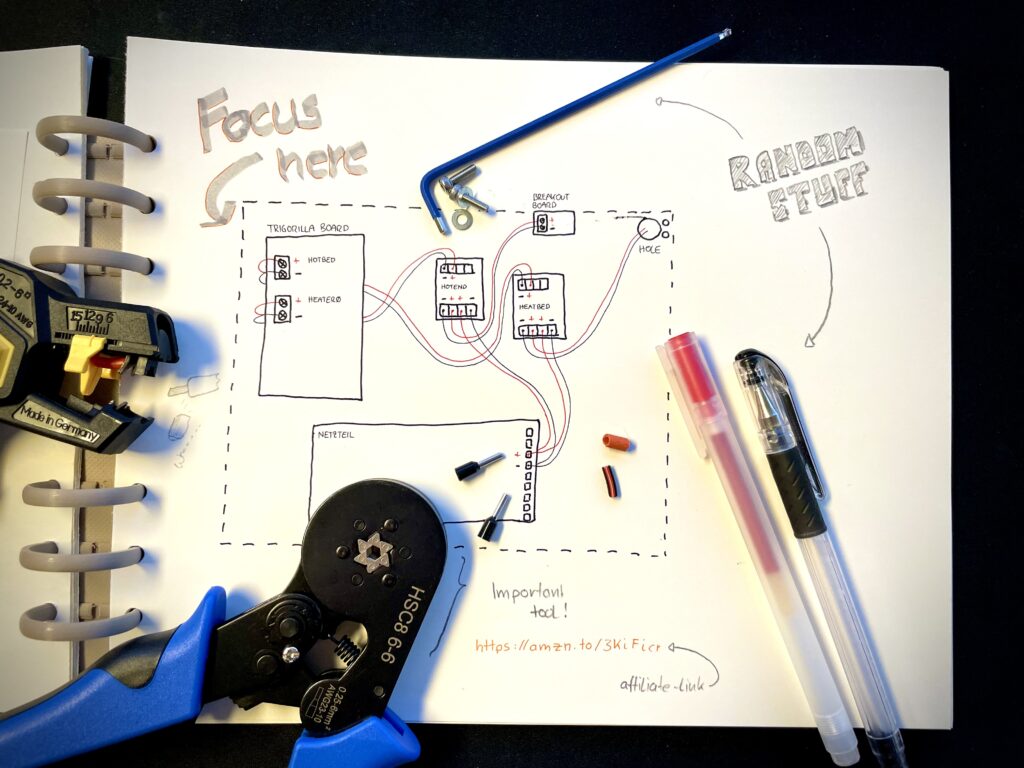
Crimpen!
Weiter oben habe ich es schon angesprochen: Die Kabelenden zu crimpen ist eindeutig nicht nur eine schlaue Wahl – laut VDE Norm in vielen Bereichen sogar Vorschrift. Ich dachte übrigens, das sei simpel. Crimpzange raus, Kabel abisolieren, Aderendhülse draufstecken, crimpen, fertig. Kannst auch quetschen sagen. Ist aber gar nicht so simpel – für einen nicht-gelernten Elektriker wie mich.
Hier also die Kurzfassung:
Es gibt internationale Normen was Kabeldurchmesser und Aderquerschnitte betrifft. Passend dazu gibt es Farbkodierungen. Diese können sich aber von Land zu Land unterscheiden. Mehr dazu liest Du z.B. in diesem Blogartikel. Einzig darüber, dass es wichtig ist, sich darüber einig zu sein, dass das wichtig ist, sind sich die Länder einig. Entsprechend gibt es verschieden farblich kodierte Aderendhülsen passend zu den verschiedenen Kabeln (und länderübergreifende Übersetzungstabellen). Und wenn Du die exakten Spezifikationen Deiner Kabel gerade nicht zur Hand haben solltest, wäre die Idee grundsätzlich die: Benutze eine Hülse, in dessen Isolation das Kabelende inkl. Ummantelung reinpasst und in dessen Metallhülse die abisolierten Litzen bestmöglich passen. Dann isoliere genau so viel Mantel ab, dass die Litzen bis zum Ende der Hülse reicht. Abschließend: Hülse draufstecken, crimpen, fertig. Wichtig: Nicht die Litzen verdrillen. Das verändert die Mechanik und auch den Leiterquerschnitt – beides willst Du nicht.
Warum macht man das? Nun zum einen läufst Du nicht Gefahr, dass sich einzelne, feine Adern beim Verschrauben verselbstständigen und Kurzschlüsse verursachen. Und zum anderen entsteht durch richtiges Crimpen eine gasdichte Verbindung. Das bedeutet, dass ein Oxidieren des Leiters in der Hülse verhindert wird, da zwischen den einzelnen Drähten nach dem Crimpen nahezu keinerlei Hohlraum mehr existiert.
Hier mal ein paar Bilder dazu:
![]() | ![]() | ![]() |
![]() | ![]() | ![]() |
![]() | ![]() | ![]() |
An dieser Stelle gehen die Meinungen etwas auseinander und ich empfehle folgendes nicht, berichte aber darüber, was ich gemacht habe: Ich habe die gecrimpte Hülse gekürzt, nachgecrimpt und dann gesteckt. Ich bin mit dem Ergebnis sehr zufrieden.
![]() | ![]() |
Ein neues Druckbett-System
Die Tatsache übrigens, dass ich plane, meine UltraBase durch ein neues Druckbett-System auszutauschen, hatte u.a. zur Folge, dass ich nicht so sparsam mit den stromführenden Kabeln umgehen musste (war ja genug übrig). Hier aber ein Tipp für Dich, falls Du planst, auch die Enden der Kabel mit Aderendhülsen auszustatten, die in dem Breakout-Board mit den vielen Anschlüssen führen, an die von Außen diverse Kabel gesteckt sind: Mach das, bevor Du die Adapterplatte mit den MOSFETs einbaust. Anderenfalls könnte es schwierig werden, da Du vermutlich nicht mehr genug Platz für einen konventionellen Schraubendreher hättest, um an die Schraubklemmen heranzukommen.
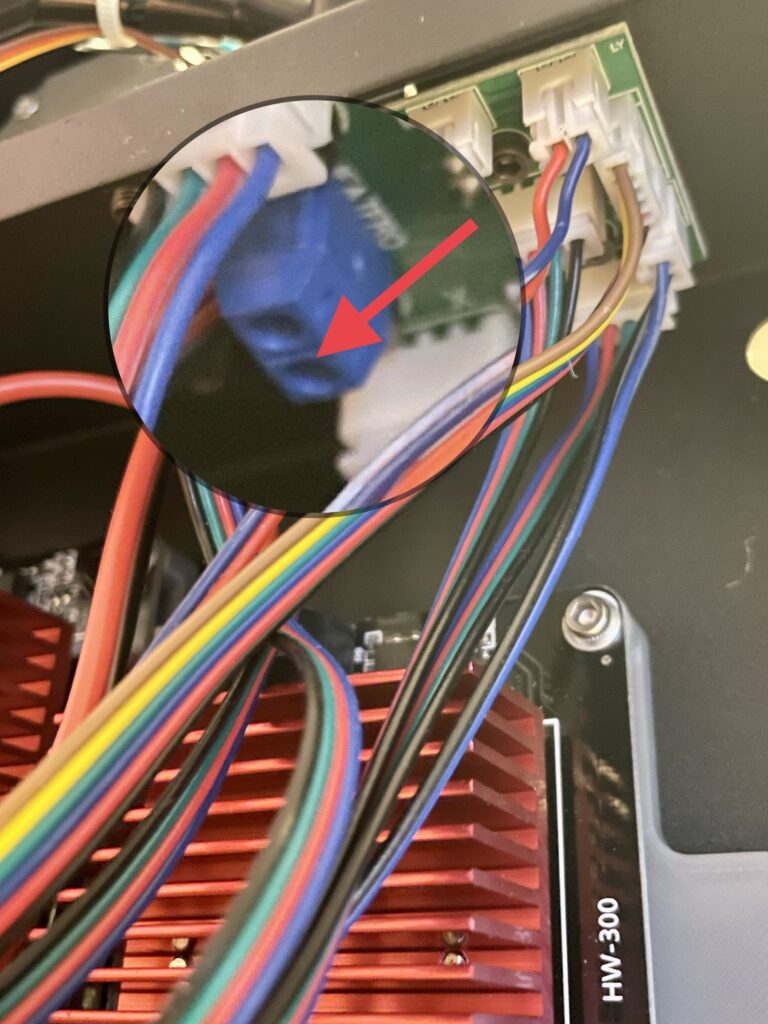
Ansonsten sind nun auch die Anschlüsse am Trigorilla Board mit den MOSFETs verbunden:
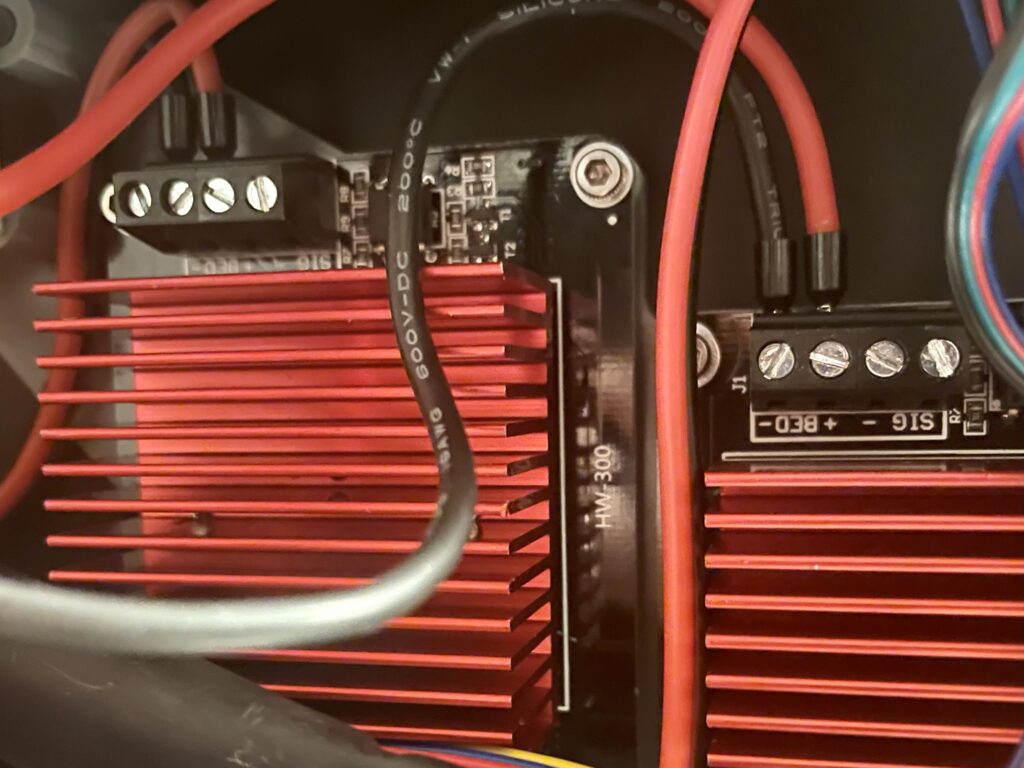
Das Netzteil
Was u.a. noch fehlt, ist die Spannungsversorgung für die Komponenten, die die MOSFETs schalten soll. Die kommt natürlich vom Netzteil und Du hast in Deinem AnyCubic i3 Mega zwei Anschlüsse frei für Plus und Minus. Das Problem: Du musst jeweils zwei MOSFETs daran anschließen.
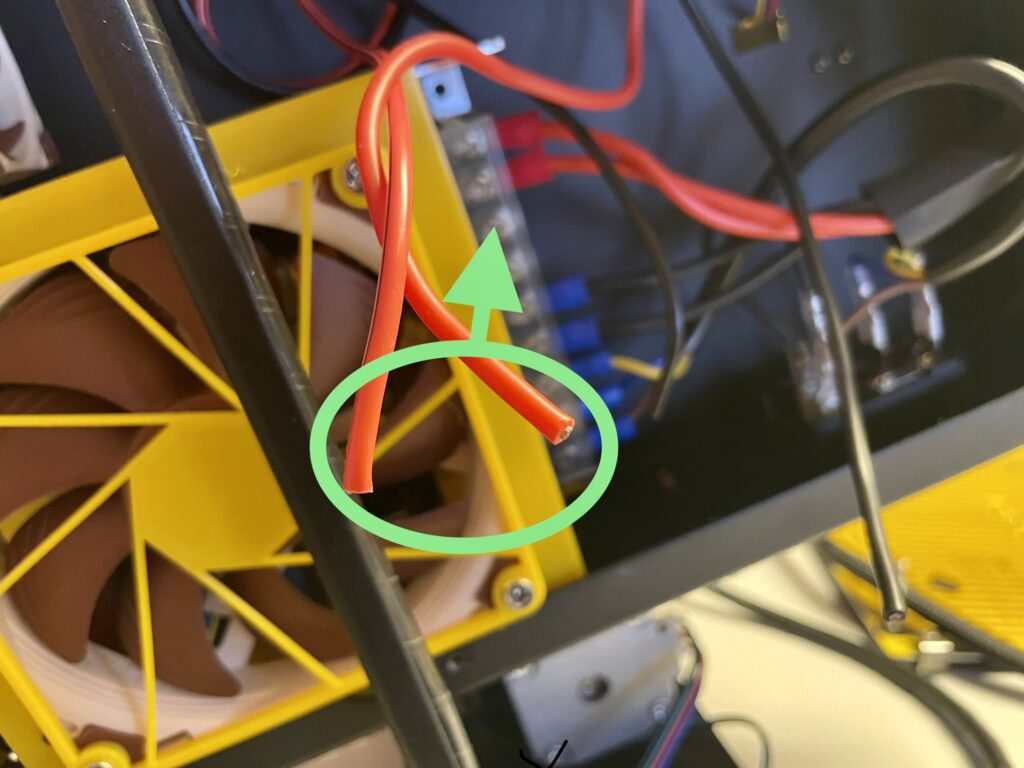
Wenn Du Dir die anderen Kabel anschaust, stellst Du fest, dass diese auf Gabelkabelschuhe gequetscht sind. Die funktionieren etwas anders als Aderendhülsen. Sie sehen aus wie kleine Hufeisen, an deren einem Ende eine flexibel ummantelte Hülse angebracht ist. Diese wird inkl. der Ummantelung mittels einer speziellen Crimpzange auf die abisolierten Kabel gepresst. Und obwohl es sog. Doppel-Aderendhülsen gibt (wahlweise auch Zwillings- oder englisch: Twin-Aderendhülsen genannt), die die Aufnahme zweier Kabel vorsehen, gibt es so etwas scheinbar nicht für Gabelkabelschuhe – oder Schuhe im Allgemeinen (ist auch einfach zu erklären: In einen Schuh passt grundsätzlich immer nur ein Fuß…).
Was also tun (, sprach Zeus, die Götter sind…)?
An dieser Stelle bin ich nicht sicher, was Elektriker sagen würden. Ich in meinem Fall habe die beiden Adern jeweils mit regulären Aderandhülsen versehen und dann von beiden Seiten eingeführt und verschraubt. Damit pressen von unten und von oben zwei quadratische Plättchen auf die Adern. Stabil ist es allemal, allerdings nehme ich an, dass sich dadurch auch die Kontaktfläche und damit der Kontaktwiderstand verändert. Das wiederum führt zu einer anderen Verteilung von Wärme. Da hier aber “nur” ein 3D Drucker betrieben wird und an anderen Stellen auf dem Board tw. mit ganz anderen Mitteln gearbeitet wird (ohne dass laufend alles in Flammen aufgeht), gehe ich davon aus, dass das kein wirkliches Problem darstellt.
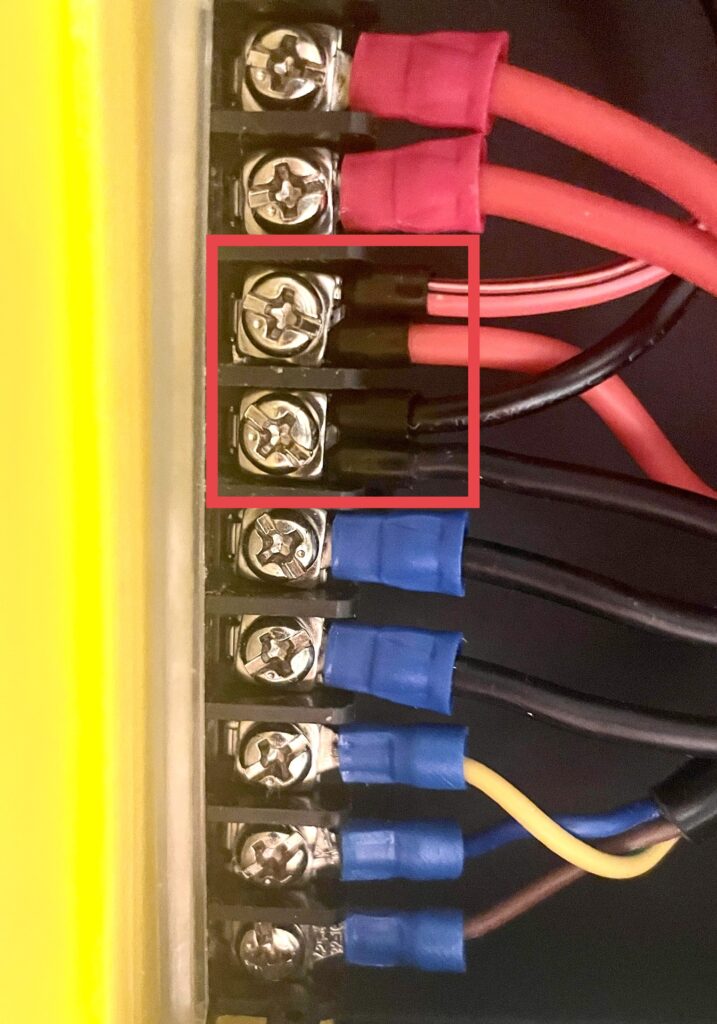
Im übrigen sind Aussagen wie “gehe ich davon aus” natürlich nicht haltbar. Daher rufe ich alle Elektriker, die diesen Beitrag lesen, dazu auf einmal zu erläutern, wie sie an die Sache herangehen würden – idealerweise konform zur VDE, aber immer im Kontext “3D Drucker” (sprich: Einfach auch mal die Kirche im Dorf lassen… hier wird keine Rakete für den Transport von Menschen zum Mars gebaut).
Ergebnis
Nachdem nun also die beiden externen und sehr gut passiv gekühlten MOSFETs eingebaut sind und alles grundsätzlich soweit verkabelt ist, fehlt nur noch eines: Der Anschluss des neuen Druckbett-Systems. Das ist nämlich noch nicht eingetroffen. Dieser letzte Schritt folgt also noch.
Bis dahin lässt sich aber folgendes sagen – und ich weiß, dass einigen diese Frage schon seit einigen Absätzen auf der Zunge brennt – die OnBoard-MOSFETs sind damit nicht außer Dienst gestellt. Allerdings schalten sie nun keinen hohen Stromfluss mehr, sondern nur noch die externen MOSFETs. Und die sind… safe. Und sehen mächtig hübsch aus mit ihren glänzenden Passiv-Kühlgerippen, den schicken, schwarzen Boards und großräumigen Schraubklemmen, die viel Platz für passende Aderendhülsen haben. Da möchte man direkt einziehen!
Achja: Und wer das alles in Bewegtbild mit Tonspur erleben möchte, schaut sich einfach das Video von Philipp Hubert auf YouTube an. Ist schon ein paar Jahre alt (das Video… Philipp aber auch) und geht an einigen Stellen nicht so sehr ins Detail wie dieser Text hier,… hat aber bessere Kameraschnitte und eine optimale 3D-Ansicht auf die Komponenten.
In diesem Sinne: Bis zum nächsten Mal!
2 comments on “[3D-Druck] Mit externen MOSFETs die Brandgefahr mindern”